Gusskern aus dem 3D-Drucker – Carl GmbH reduziert die Herstellkosten
Ein x400 3D-Drucker reduziert bei dem Brennereianlagen-Hersteller Carl GmbH die Herstellkosten. Die Carl GmbH fertigt seit über 140 Jahren Anlagen für Brennerei, Destillation und Brauerei. Die Schwaben liefern und installieren ihre Anlagen in der ganzen Welt. Als der Auftrag einer irischen Whisky-Brennerei kam, ging man neue Wege und setzte auf Kupferguss. Der Gusskern dafür wurde mit einem x400 3D Drucker von innovatiQ gefertigt.
Gusskern für eine Whisky-Brennerei
Die neue Anlage sollte in zwei Brennkesseln über 10.000 Liter Maische fassen. Die Herausforderung war, in dieser Größenordnung eine schöne Verbindung zwischen dem Kessel und der Kühlung herzustellen. Verwendet wird dafür ein Kupfer-Rohr, das allerdings eine konische und gebogene Form aufweist und an beiden Enden Flansche hat. Ein Bogen hat etwa ein Format von 97 x 63 cm und am größeren Flansch einen Rohrdurchmesser von 43 cm.
„Der normale Weg wäre gewesen, das Kupfer mit Hammer und Amboss in ca. sechs Wochen Arbeit per Hand in Form zu dengeln“, erklärt Thomas Keller, der das Projekt auf der technischen Seite unter seiner Fittiche hatte. Die Kosten dafür: mehrere Zehntausend Euro, und das mal zwei, da jeder Kessel einen Bogen zum Kühler benötigt. So kam die Alternative Kupferguss ins Spiel. Das Hauptproblem fasst Keller zusammen: „Wie komme ich kostengünstig an eine Form?“ Fräsen bzw. fräsen lassen einer Form hatte sich bei der Kalkulation als ebenso unwirtschaftlich herausgestellt wie das Dengeln per Hand.
Lösung: Gusskern für den Sandguss mithilfe eines 3D-Druckers
Nach einigen Recherchen kam Thomas Keller zu dem Schluss, dass sich ein Versuch lohnen würde, den Gusskern für den Sandguss mithilfe eines 3D-Druckers herzustellen. So machte er sich seinen Angaben zufolge auf die Suche nach einem 3D-Drucker mit dem besten Preis-Druckraum-Verhältnis. Gekauft wurde schließlich ein x400-Modell des deutschen Herstellers innovatiQ. Der 3D-Drucker druckt Objekte bis zu einer Größe von 400 x 400 x 350 mm, was einem Volumen von 56 Litern entspricht.
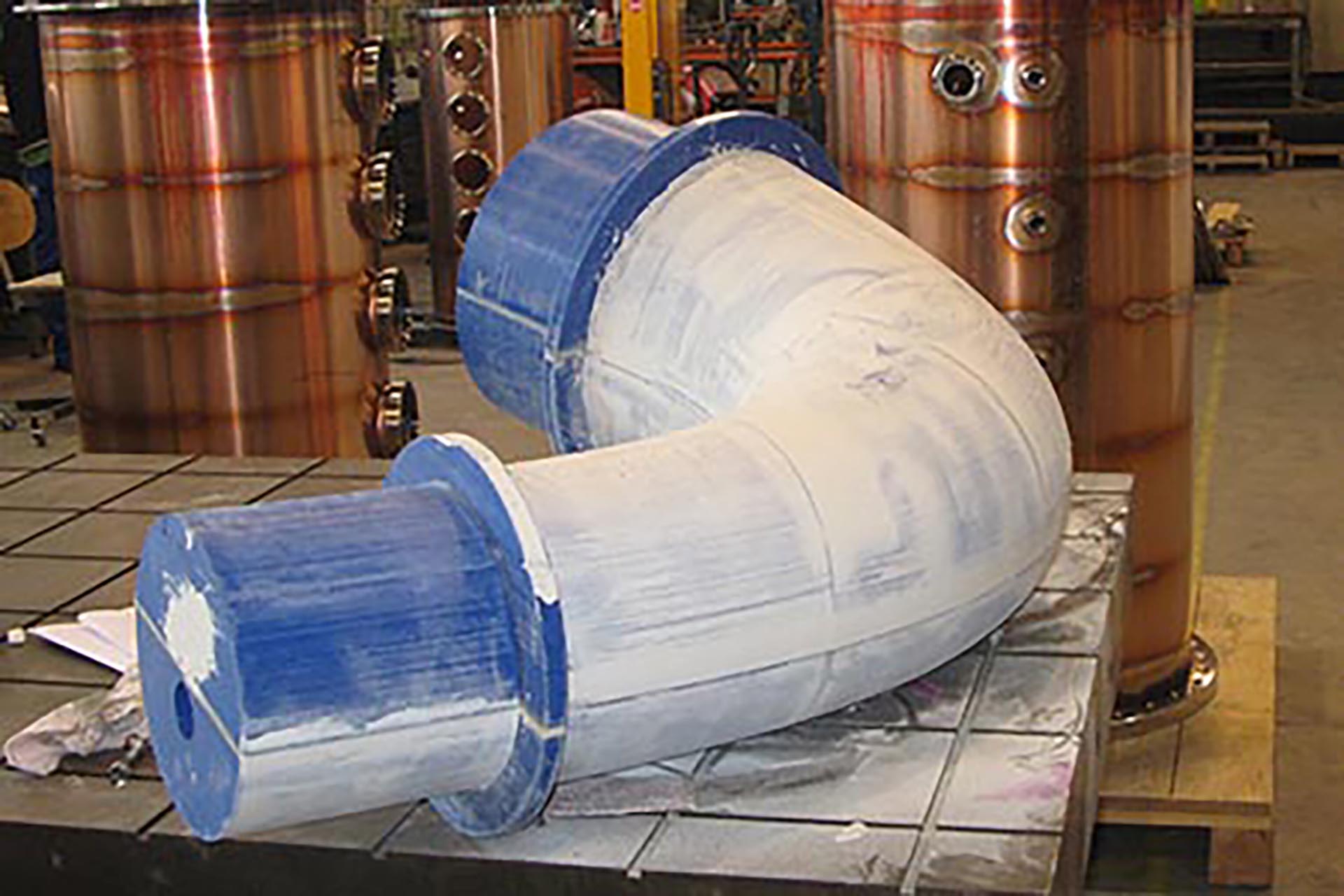
Herstellung des Gusskerns im Prozess
Da sich die beiden Bögen nicht im Ganzen drucken lassen, wurden sie in 22 bzw. 16 Teile zerlegt. So hatten sie eine druckbare Größe. Der gedruckte Gusskern besteht aus zwei Hälften. Die Einzelteile werden zusammengeklebt und verspachtelt. Schließlich wird das gesamte Modell wieder abgeschliffen. Bereits in der Konstruktion der 3D-Druck-Modelle wurden Ansätze für die anschließende Wachsfolie berücksichtigt, die als verlorenes Modell später ausgeschmolzen wird. Nach dem Ausschmelzen des Wachses wird das flüssige Kupfer gegossen. So entsteht durch 3D-Druck und Sandguss ein individuell geformter Kupferbogen.
Keller druckte seine Gusskerne mit PLA-Filament. Diese Polymilchsäuren (Polyactide) werden bei 210°C geschmolzen und in dünnen Schichten von ca. 0,1mm zu einem 3D-Objekt aufgebaut. „PLA lässt sich einfach drucken und liefert sehr zuverlässige Ergebnisse“, so Keller zu seiner Wahl. Mit einer Geschwindigkeitseinstellung von 50 mm/s und 250%, also 125 mm/s, war ein Teil nach 2,5 Tagen Druckzeit fertig.
Der neue Fertigungsprozess rechnete sich. Mittlerweile steht ein zweiter x400-Drucker bei der Carl GmbH.