Zurich Opera House relies on 3D printers from innovatiQ for props and mold making.
With 12 new productions on the main stage every year, numerous revivals, concerts, song recitals, a wide range of young talent programs and over 300 performances, Zurich Opera House is the largest cultural institution in Switzerland and also one of the most productive houses in Europe. For the events, there are various workshops and studios where the detailed decorations and costumes are painstakingly and lovingly produced. This is supported by the x400 3D printer from innovatiQ. Swiss reseller KVT-Fastening has supported the Zurich Opera House in this process on site in Switzerland.
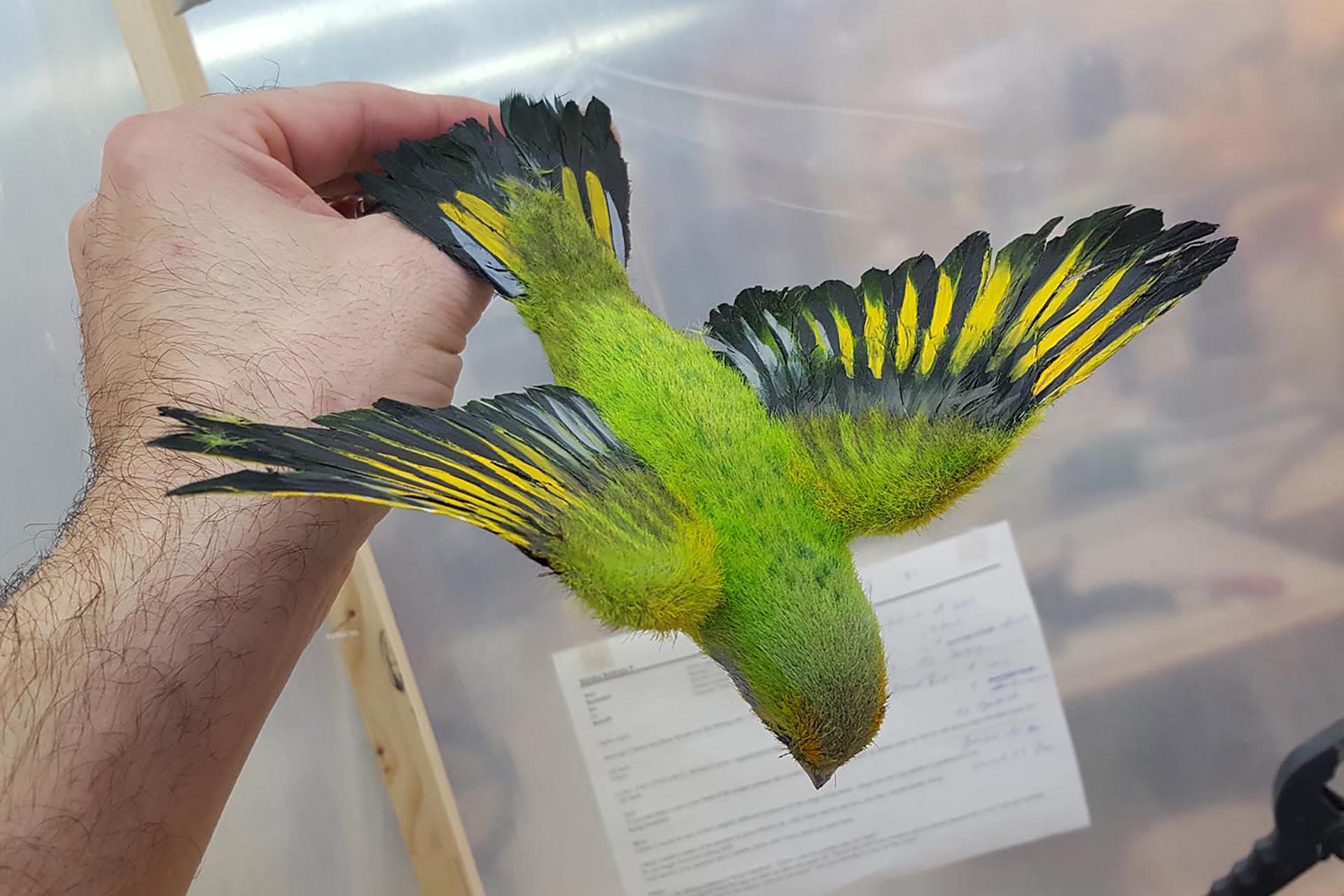
The range of applications for additive manufacturing technology is diverse – the 3D printer is used primarily for the production of props and for mold making. “Often the wishes and ideas of costume and set designers are very diverse and sometimes unusual,” says Andreas Gatzka, Head of Theater Sculpture and Sculpture at Zurich Opera House, “so it often happens that props can’t be bought like that, and that’s when the 3D printer comes into play.” First, the objects are designed in the 3D modeling program and then printed. These objects are then further processed, for example flocked, painted or glued, and used as the final product on stage.
The innovatiQ x400 is also used for mold making. For the character of the Sugar Plum Fairy in the ballet “The Nutcracker,” for example, there was a request for ultra-light cupcakes to be mounted on the top of tutus. In a first step, the cups of the cupcakes were created in a 3D modeling program. Different designs with a wide range of proportions were tested to find the ideal design. These cups were then produced with the innovatiQ x400 and served as the original mold for the production of silicone negatives. These in turn were used to reproduce the cups from temperature-resistant casting resin as thermoforming tools. The final cups were thermoformed with very thin and thus lightweight polystyrene film.
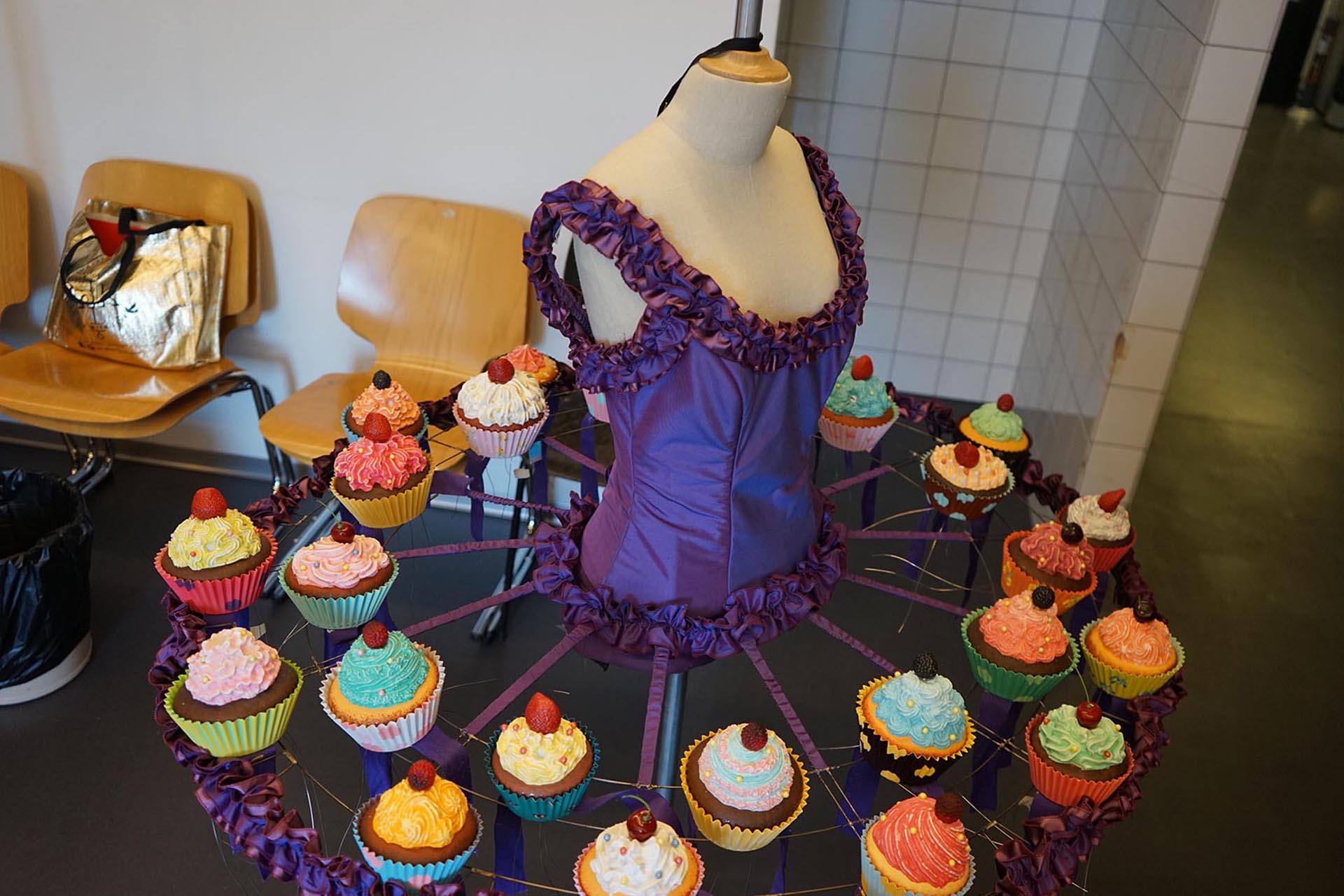
Mr. Gatzka answers the question of how the Zurich Opera House got its own 3D printer with a smile: “Through curiosity, interest and fascination! We have been using the technology itself for a few years now. But we’ve always had external suppliers for that until now.” With its own 3D printer, however, the opera house can be even more flexible and get creative itself. This saves costs and also time due to the shorter processes. Mr. Gatzka sees further advantages as follows: “The general advantages are very great. Special wishes of stage and costume designers can be realized quickly as well as a short-term change of the objects, for example bigger, smaller, longer, shorter, as the case may be.” Florian Bautz, Managing Director of innovatiQ, is pleased when the customer is satisfied: “It’s great to see how many areas our machines are already being used in. The trend is definitely towards the adoption of additive manufacturing, because the new technology offers many advantages, such as the ability to reduce weight and produce complex structures, or the greater flexibility of molds and shorter production cycles. Another advantage, which can also be seen nicely in this project, is that one-off productions are now profitable. In conventional production, a single piece costs a fortune and only pays off when it can be manufactured by the thousands in a series production.”
In terms of materials, the opera house is currently relying exclusively on PLA, as it is also well suited for beginners and is easy to handle. The wide variety of colors and effects plays a major role. It is also flame retardant, an important criterion in the theater sector. The finished printed PLA product can also be post-processed very well. “For the future, we would also like to use other materials, such as ABS, PET-G, nylon or elastic filaments,” says Mr. Gatzka.
Severin Struck, Sales Engineer at KVT-Fastening, provided the Zurich Opera House with the necessary support in selecting the optimal 3D printing device: “I was allowed to support Mr. Gatzka in his project. Through our position as an Additive Manufacturing Center, KVT-Fastening offers 3D printing devices from various manufacturers, among others. In the case of the Zurich Opera House, it was quickly clear that the innovatiQ x400 with the FFF process was the right device. In addition to 3D printers, however, KVT-Fastening’s Additive Manufacturing Center also provides products such as materials, accessories, software and services. We can support customers from the design phase to the production of parts and advise them on the selection of equipment and related manufacturing technologies. This enables us to offer our customers the solution that is perfectly tailored to their needs. We were also able to offer a complete package for the Zurich Opera House. So it was a pleasure to assist the opera house with consulting, commissioning, training and maintenance contracts.”
The opera house came to the German 3D printer manufacturer innovatiQ as follows, reports Mr. Gatzka: “I googled for a 3D printer that had a print space that roughly allows the printing of a human head with the two shoulders. That’s when the x400 from innovatiQ came up. When I visited the x400 at the KVT-Fastening booth at the AM Expo in Lucerne, the machine made a very good impression on me, which was confirmed by Internet research (testimonials) and a visit to the reseller, KVT-Fastening. Other criteria were two print heads, which allows printing with separate support material, as well as a wide variety of materials in general.” With the innovatiQ 3D printers, customers benefit from an open material platform, which means that a wide range of materials have already been tested and approved for printing on the innovatiQ machines, and other materials can also be tested. This is up to the customer. “The x400 has a very compact and robust design. It therefore just fits super in our studio! It was also very important for us to have a local contact (and not just a salesperson) in Switzerland, which is the case with the innovatiQ reseller, KVT-Fastening. And we are super satisfied!”
Currently, the x400 3D printer is already being used successfully in a number of areas, and the opera house can very well imagine that the “new helper” will sooner or later become an important component for further projects. The new team member is generating more and more interest and enthusiasm.